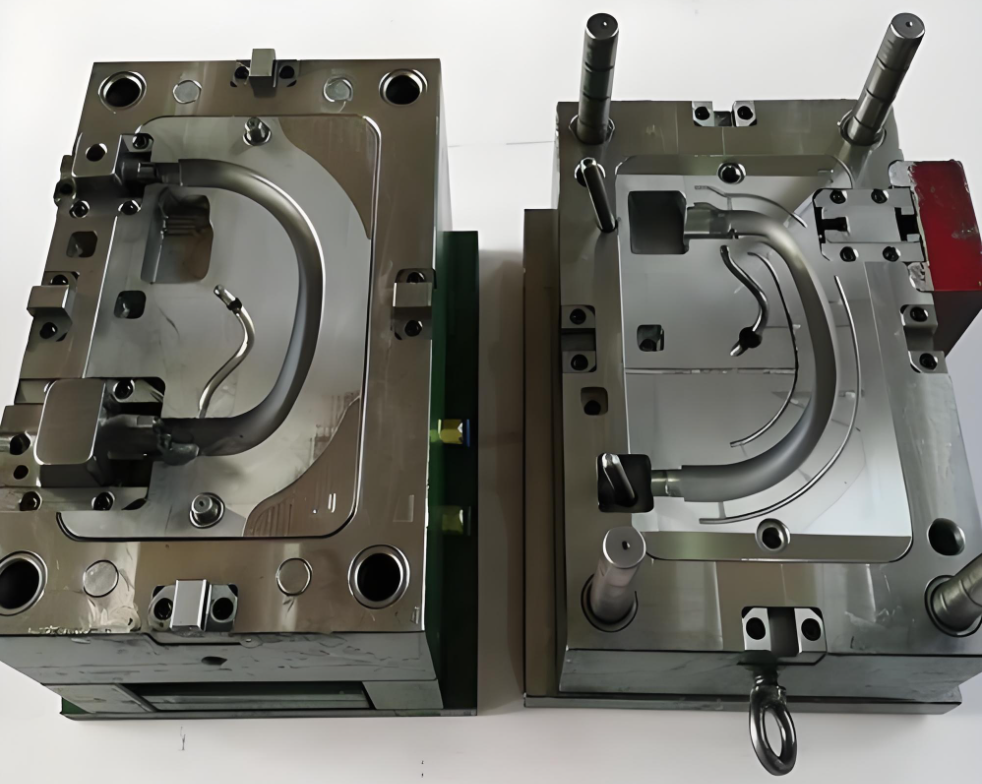
Basic principles of gas assisted molding:
Gas assisted molding is divided into four stages: mold closing, resin melt injection molding, gas injection, gas holding pressure, gas releasing and mold opening, and part ejection.
(1) Resin melt injection molding: Plastic melt is injected into the mold cavity, about flowing 60% -95% of the mold cavity. The pre injection amount varies depending on the process selection during actual production: insufficient material gas assisted, full material gas assisted,; It is also related to product design and appearance requirements
(2) Gas injection: High pressure inert gas (usually nitrogen) is injected into the interior of the melt, and the front edge of the melt flow continues to flow forward under the push of the high-pressure gas, eventually filling the entire mold cavity; Or the internal materials are pushed into the overflow area by high-pressure gas. The goal is to create a hollow cross-section inside the component using high-pressure gas.
(3) Gas pressure maintenance: The gas maintains a certain pressure to gradually cool the workpiece under uniform pressure maintenance. At this stage, the gas is pressurized from the inside out to ensure that the outer surface of the product is tightly attached to the mold wall
(4) Gas discharge, mold opening, and part ejection: After pressure holding and cooling, the part has sufficient rigidity and strength before releasing gas; After further cooling, the workpiece is molded and then ejected.